
Work order and inventory management software is crucial for optimizing maintenance and operational workflows. Without an efficient system, businesses risk delays, unnecessary costs, and operational inefficiencies that can slow growth. The right software solution can streamline these processes, helping companies prevent bottlenecks, maintain accurate records, and keep maintenance schedules on track. Let’s dive into everything you need to know to build work order and inventory management software using Knack’s no-code platform.
Key Takeaways:
- Work order and inventory management software is a tool that helps organizations efficiently track, schedule, and manage maintenance tasks while monitoring inventory levels to ensure seamless operations.
- Work order and inventory management software are combined to streamline maintenance processes and ensure the necessary inventory is available for timely repairs. This minimizes downtime and improves operational efficiency.
- Work order and inventory management software should include features for preventive and predictive maintenance, mobile accessibility, real-time updates, CMMS, and customizable workflows and templates.
Top Work Order and Inventory Management Software
With so many software solutions on the market, how do you decide which is best for your business? We’ve compared the top work order and inventory management software available to help you make an informed decision.
Knack
Knack is a powerful no-code platform that allows businesses to build custom databases and applications to streamline their operations. It’s ideal for businesses looking for flexibility and ease of use without requiring technical expertise.
Key Benefits
- Intuitive interface with drag-and-drop functionality.
- Customizable workflows for managing complex data relationships.
- Scalable solution, suitable for small to large businesses.
- Integration with popular tools like Zapier and Integromat.
Pricing
Knack offers tiered pricing starting at $19/month for the first three months of subscription.
Drawbacks
- Limited offline functionality.
MaintainX
MaintainX is a mobile-first CMMS (Computerized Maintenance Management System) designed to streamline work orders, inspections, and asset management for industries like manufacturing and facilities management.
Key Benefits
- Real-time tracking of work orders and maintenance tasks.
- Mobile-friendly interface for on-the-go task management.
- Detailed analytics for performance tracking and optimization.
Pricing
Pricing starts at $8.33/user/month.
Drawbacks
- Limited customization for unique workflows.
- It can become costly for larger teams.
UpKeep
UpKeep is a user-friendly CMMS and asset management software built for industries that need to track maintenance tasks and monitor equipment performance effectively.
Key Benefits
- Easy-to-use mobile and desktop platforms.
- Features like inventory management and preventive maintenance scheduling.
- Integrates with IoT devices for real-time equipment monitoring.
Pricing
Plans begin at $45/month for a single user.
Drawbacks
- Limited reporting customization in lower-tier plans.
- Occasional lag with large datasets.
Jobber
Jobber is a business management software tailored for service-based industries. It offers features to streamline scheduling, invoicing, and customer relationship management.
Key Benefits
- Robust scheduling tools with drag-and-drop capabilities.
- Automated client communication and invoicing.
- Integrated payment processing for seamless transactions.
Pricing
Jobber’s pricing starts at $9/month.
Drawbacks
- Limited reporting and analytics features compared to competitors.
- Some integral features require premium plans.
Must-Have Features of Top Work Order and Inventory Management Software
Work order and inventory management software is only as powerful as its features. Every business has different needs, but most of these systems should include the following:
Preventive and Predictive Maintenance Tools
Effective work order and inventory management software should offer preventive and predictive maintenance tools to help minimize unexpected downtime and extend asset life. Preventive maintenance capabilities allow teams to schedule regular checks and repairs, keeping equipment in optimal condition. Predictive maintenance, which uses data analytics to anticipate potential failures, enables teams to address issues proactively. Together, these features ensure that equipment remains reliable and can support operational needs without costly interruptions.
Mobile Accessibility and Real-Time Updates
Mobile accessibility is crucial for today’s teams, who often need to manage work orders and track inventory on the go. This allows field technicians and remote team members to access, update, and track work orders and inventory in real-time. It keeps everyone connected and ensures that the latest information is readily available, reducing delays and improving response times in the field.
Computerized Maintenance Management System (CMMS) Capabilities
CMMS allows organizations to manage assets, schedule maintenance, and generate performance reports in a centralized platform. CMMS tools provide a comprehensive view of asset health, maintenance history, and upcoming service needs. By tracking these details, teams can make informed decisions that improve asset performance, streamline scheduling, and maintain an organized record of all maintenance activities.
Customizable Workflows and Templates
Customizable workflows and templates are highly valuable for businesses needing to adapt software to their specific processes. This flexibility allows teams to build workflows that reflect their operational requirements, making it easier to implement a solution that seamlessly integrates with existing processes.
Key Benefits of Using Leading Work Order and Inventory Management Software
Wondering why you should invest in work order and inventory management software instead of tracking everything by hand? Using this software benefits businesses through the following:
Error Reduction and Improved Accuracy
One of the primary benefits of top work order and inventory management software is its ability to minimize errors and improve data accuracy. By centralizing work orders and inventory records in a single system, businesses can reduce the risk of data discrepancies and miscommunications. Automated updates ensure that all records reflect real-time information, which is essential for maintaining accurate inventory levels and efficient scheduling.
Compliance Support and Scalability
Compliance features such as customizable reporting, audit trails, and data logging enable businesses to track and document their processes, making it easier to adhere to industry standards. Scalability ensures the software can expand alongside the business, supporting more complex processes and additional users over time.
Enhanced Collaboration and Communication
Effective work order and inventory management software promotes collaboration and communication by providing a shared platform where team members can access and update information as needed. This transparency enables different departments to coordinate tasks, share updates, and manage resources collaboratively. By fostering communication across departments, the platform helps prevent miscommunications and ensures everyone involved in maintenance and inventory management is aligned.
Practical Use Cases of Work Order and Inventory Management Software
Work order and inventory management software can help streamline operations in various fields, including:
Facility Management and Maintenance
For facility managers, keeping large-scale operations organized can be challenging without the right tools. Work order and inventory management software enables facility managers to track assets, schedule maintenance tasks, and monitor overall facility performance, helping ensure smooth and efficient operations. It also helps facility managers keep up with maintenance schedules and optimize resource allocation, which is crucial for large facilities with complex operational needs.
Manufacturing and Equipment Reliability
In manufacturing, maintaining equipment reliability is crucial for avoiding costly production delays and minimizing downtime. Work order and inventory management software is a valuable tool for managing preventive maintenance schedules, tracking spare parts inventory, and ensuring that equipment is available when needed. It supports more consistent production, which is critical in competitive manufacturing environments.
Healthcare Compliance and Equipment Maintenance
Healthcare facilities rely on a range of specialized equipment that must be maintained and compliant with health regulations. Work order and inventory management software helps healthcare providers track essential medical equipment, ensure timely maintenance, and maintain a stock of critical supplies. Compliance features, such as audit trails and reporting, assist in adhering to industry standards and ensuring equipment is always ready for use.
Create a Custom Work Order and Inventory Management Solution With Knack
Knack is a powerful no-code platform that allows users to build custom software solutions regardless of their technical expertise using a visual interface, drag-and-drop functionality, and pre-built components. In this guide, we’ll walk you through three ways you can build your own work order and inventory management solution using Knack. If you don’t already have an account, sign up for our 14-day free trial to follow along!
Watch work order inventory management in Knack
Option 1: Start With a Template App
Knack offers free app templates you can customize to make development faster and easier. For this project, we recommend using either the Work Order Template or the Inventory Management Template. Here’s how:
- In the top right corner of the app builder, click “Create New App” and then “Start from template app.”
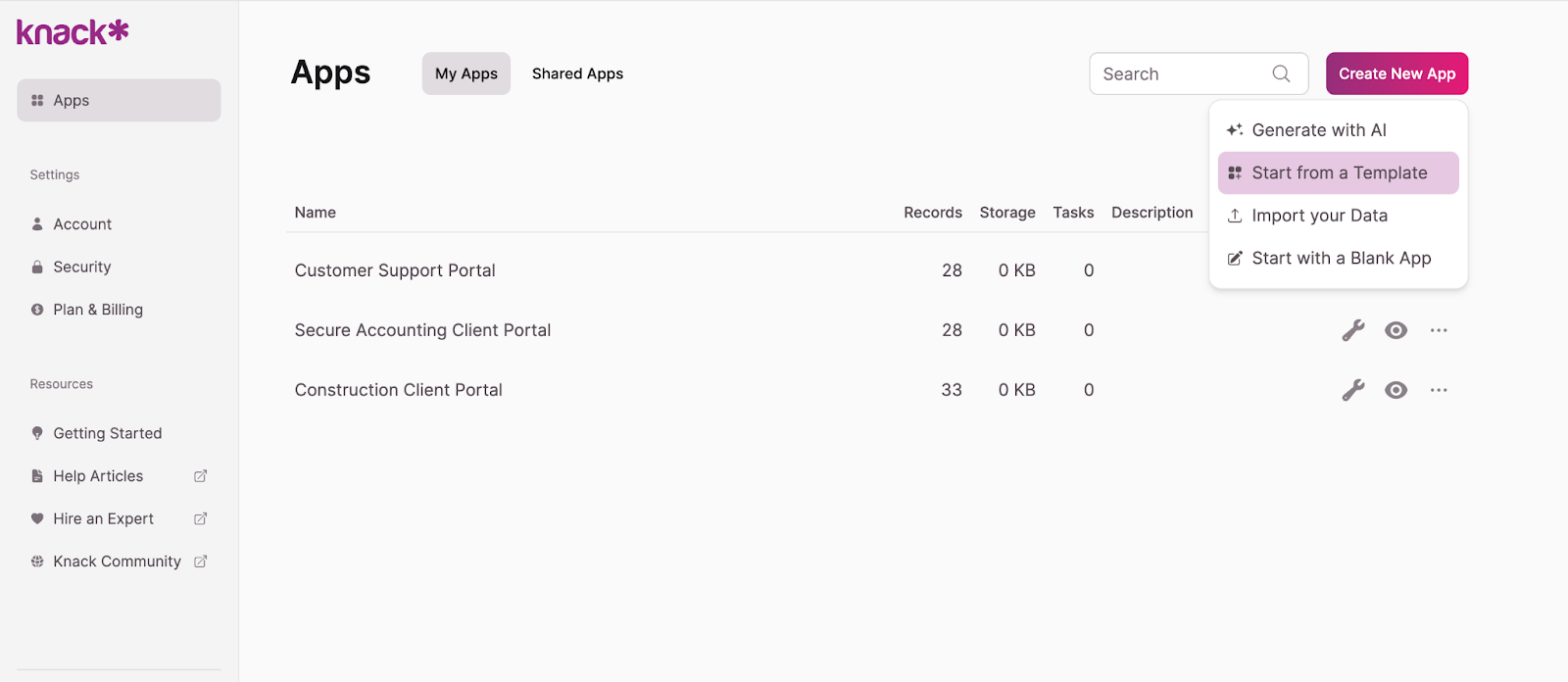
- Browse the template library to find one that best suits your needs, and click “Create App.”
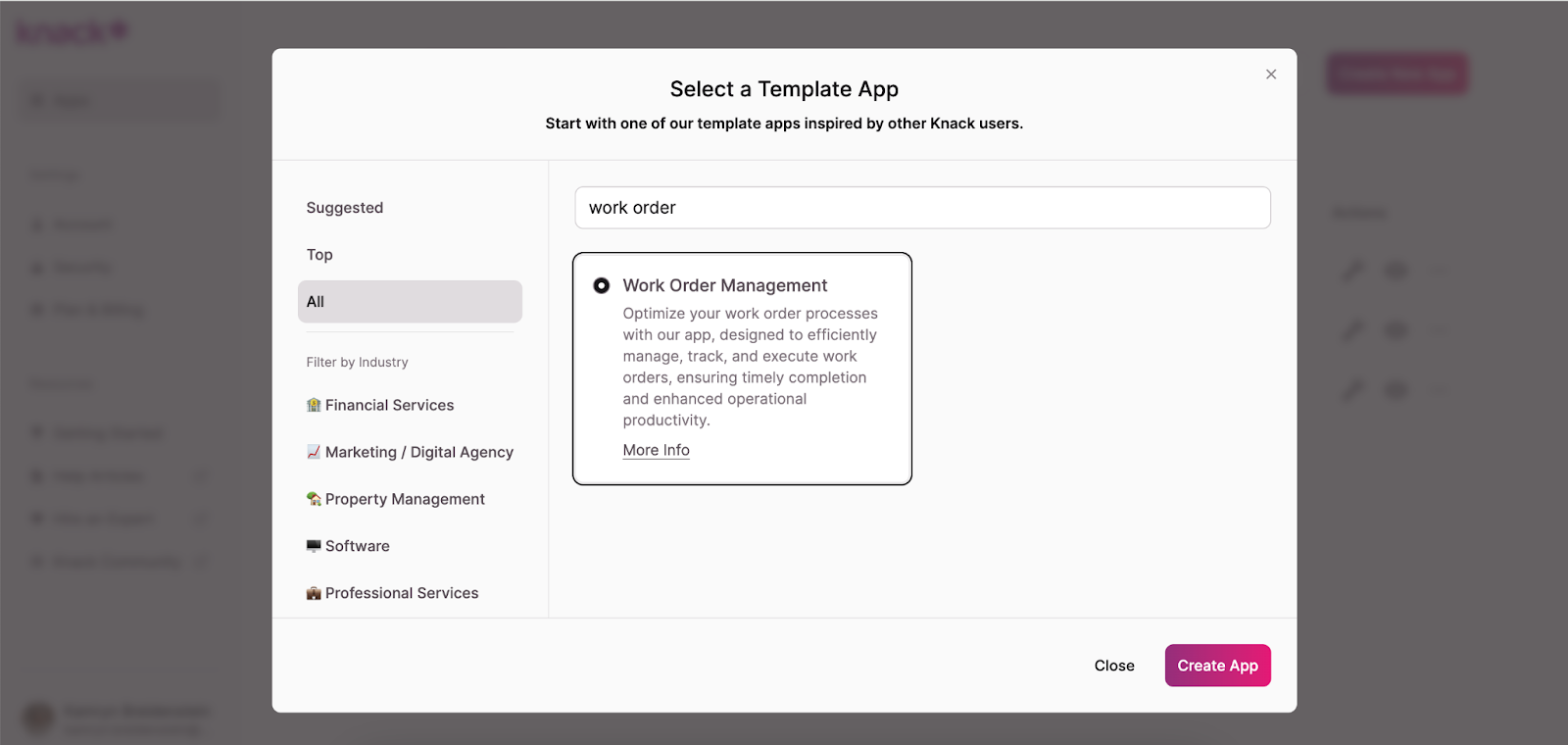
- Explore the template components and edit them to meet your requirements. Using the menu on the left, you can adjust, add, or remove tables, fields, connections, pages, and views.
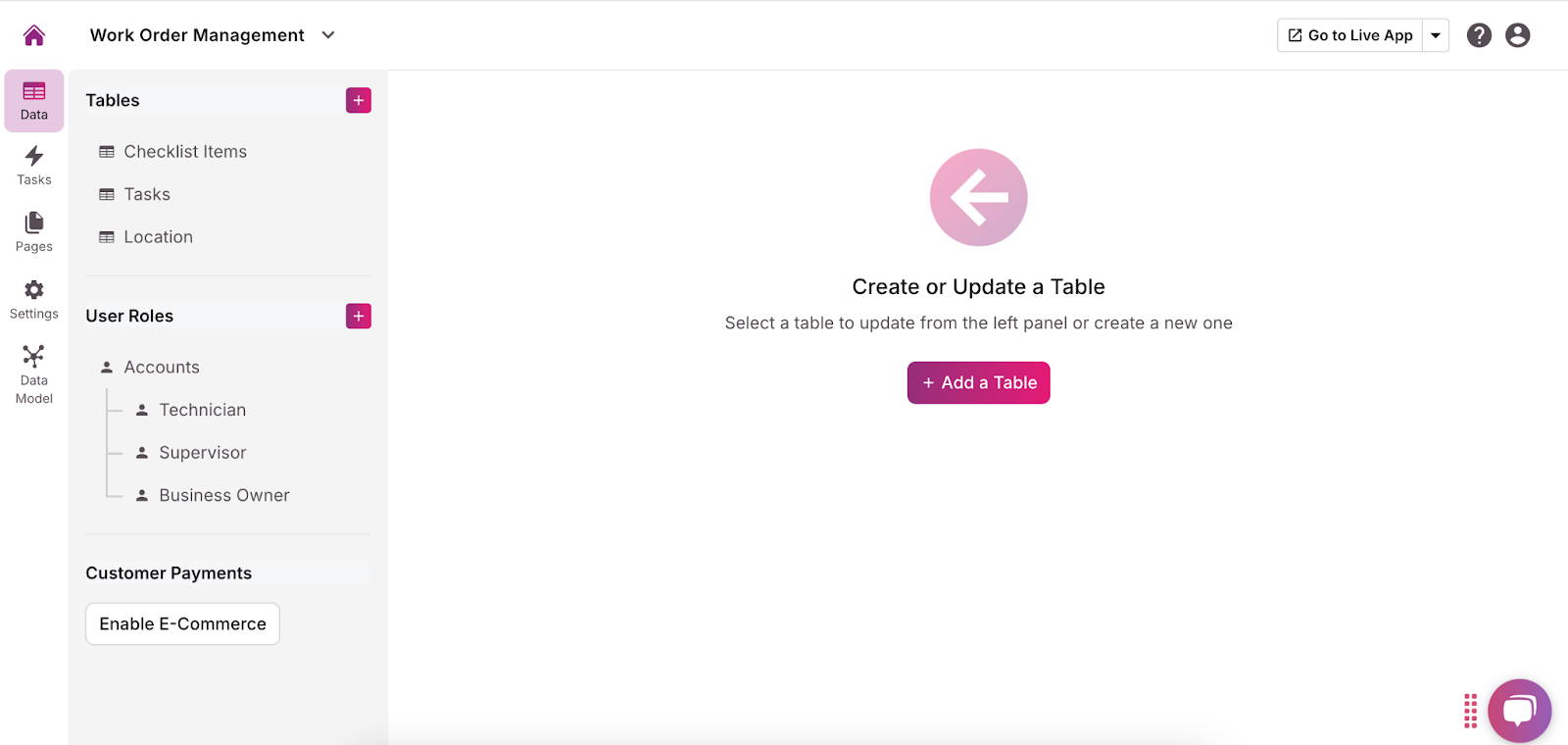
- Customize the user roles and permissions for each page by clicking the dropdown arrow and selecting “Require Login.” This allows you to choose who can access what information and functionalities.
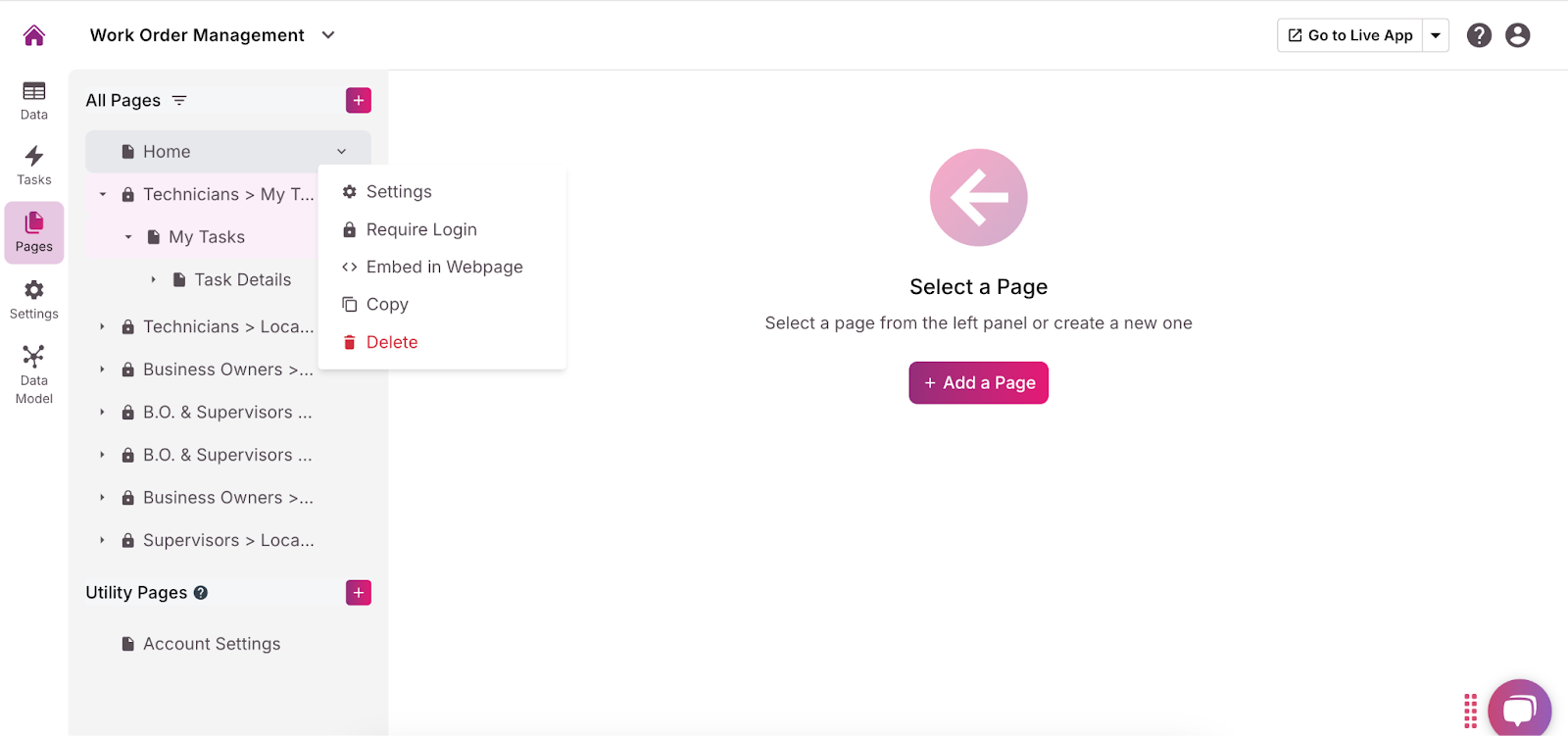
- Add any necessary integrations, like accounting or CRM software, using the “API & Code” option in the “Settings” menu. For more guidance, read this Introduction to the API article.
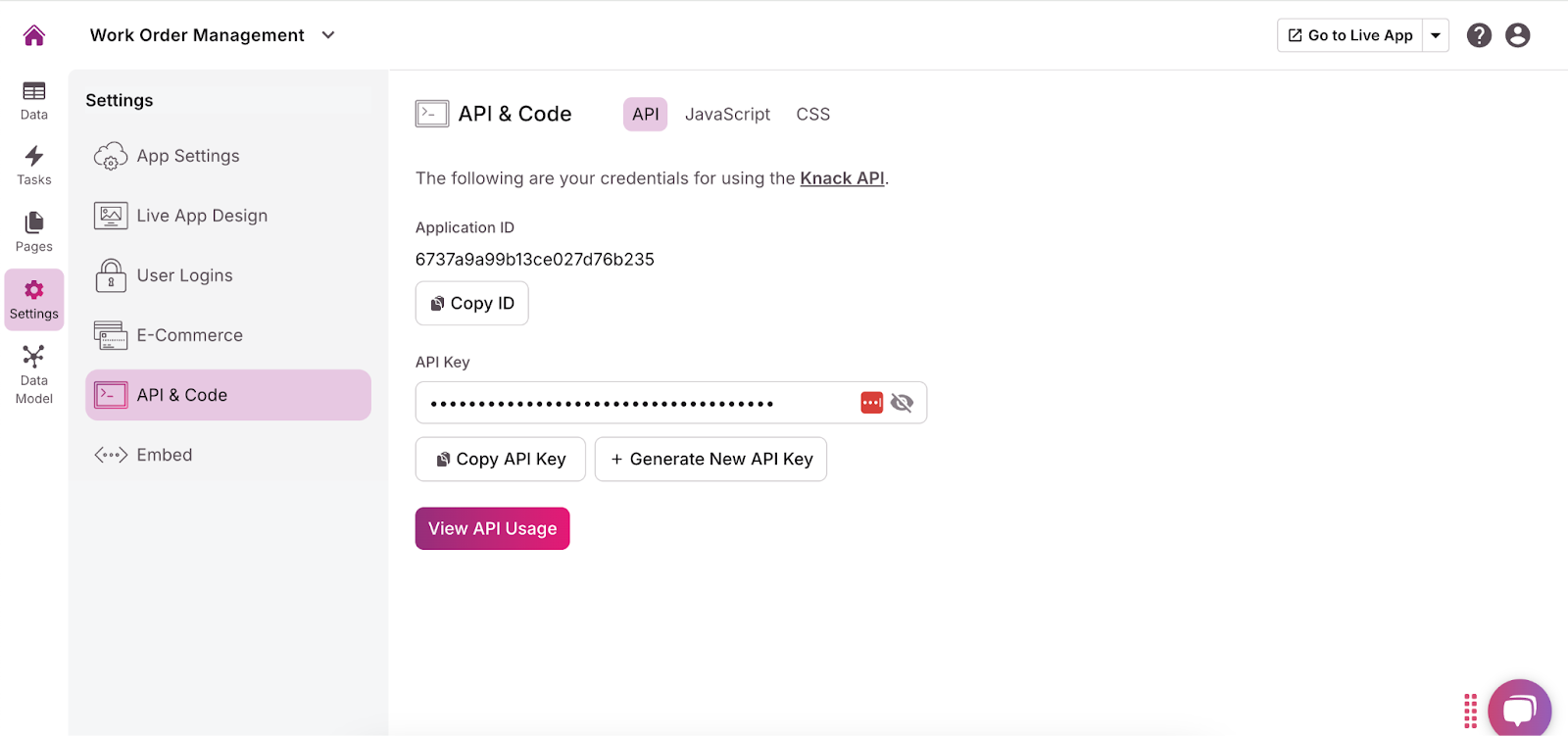
- In the menu on the left side of the builder, click “Settings” and then “Live App Design” to customize the user interface. You can add your company logo, change fonts, select colors, and more to make the portal fit your brand.
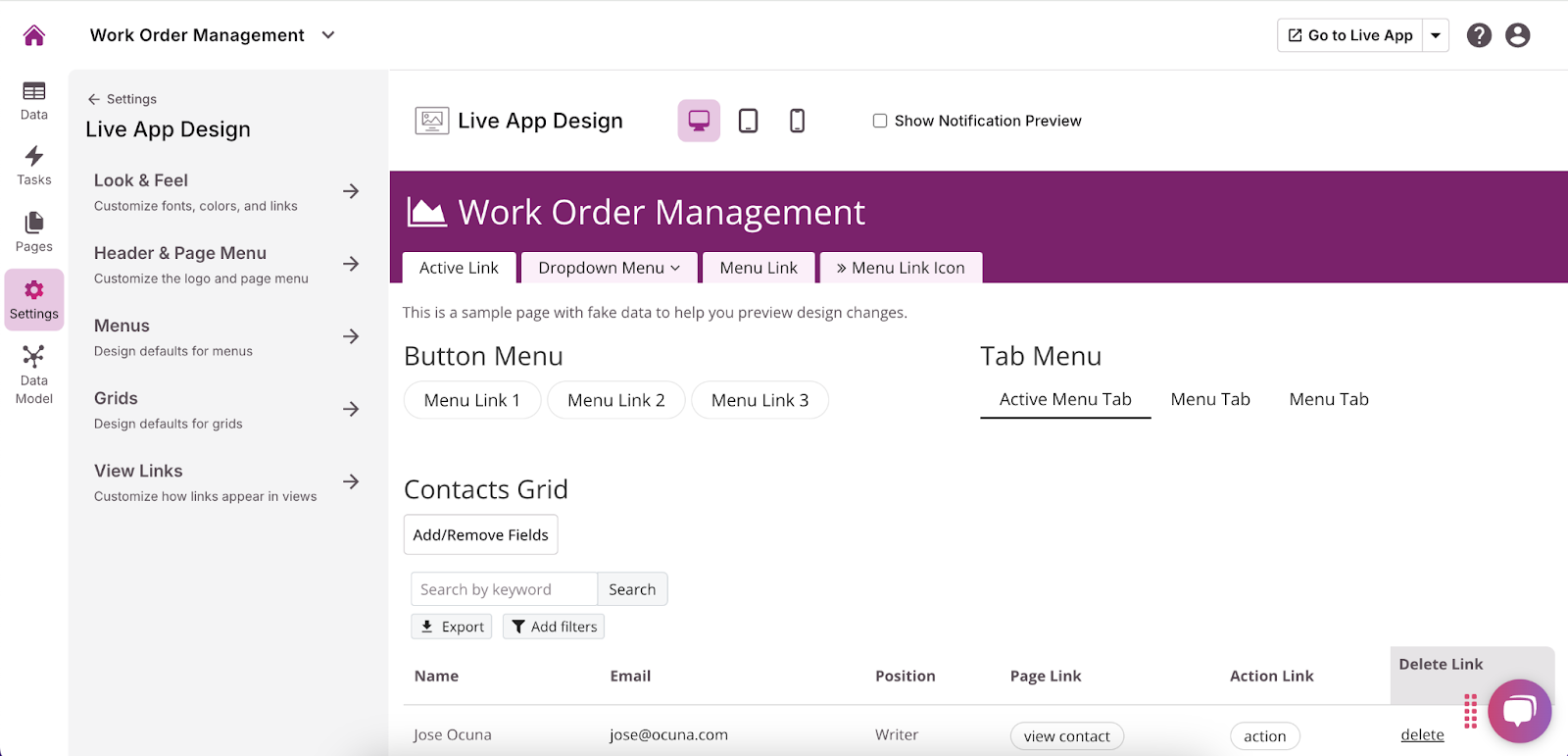
- Navigate to the “Records” section and import any existing inventory data into your tables.
Option 2: Use Our AI Builder
Knack also has a free AI app builder that offers a great starting point for building custom software. Follow these steps to get started:
- In the top right corner of the app builder, click “Create New App” and then “Start with AI.”
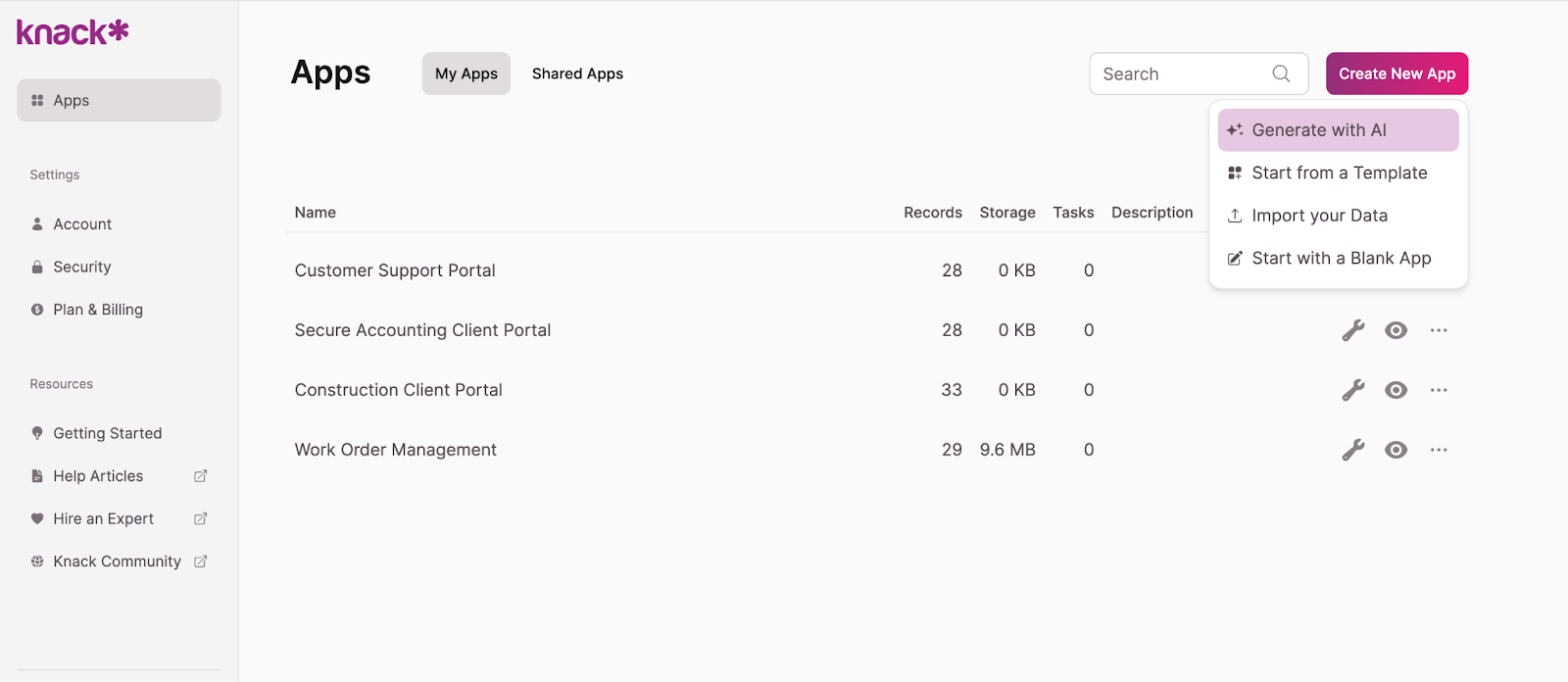
- In the pop-up, describe the solution you’re making. For example: “A manufacturing work order and inventory management system with preventive and predictive maintenance, real-time updates, and CMMS capabilities.” The AI will suggest an initial structure.
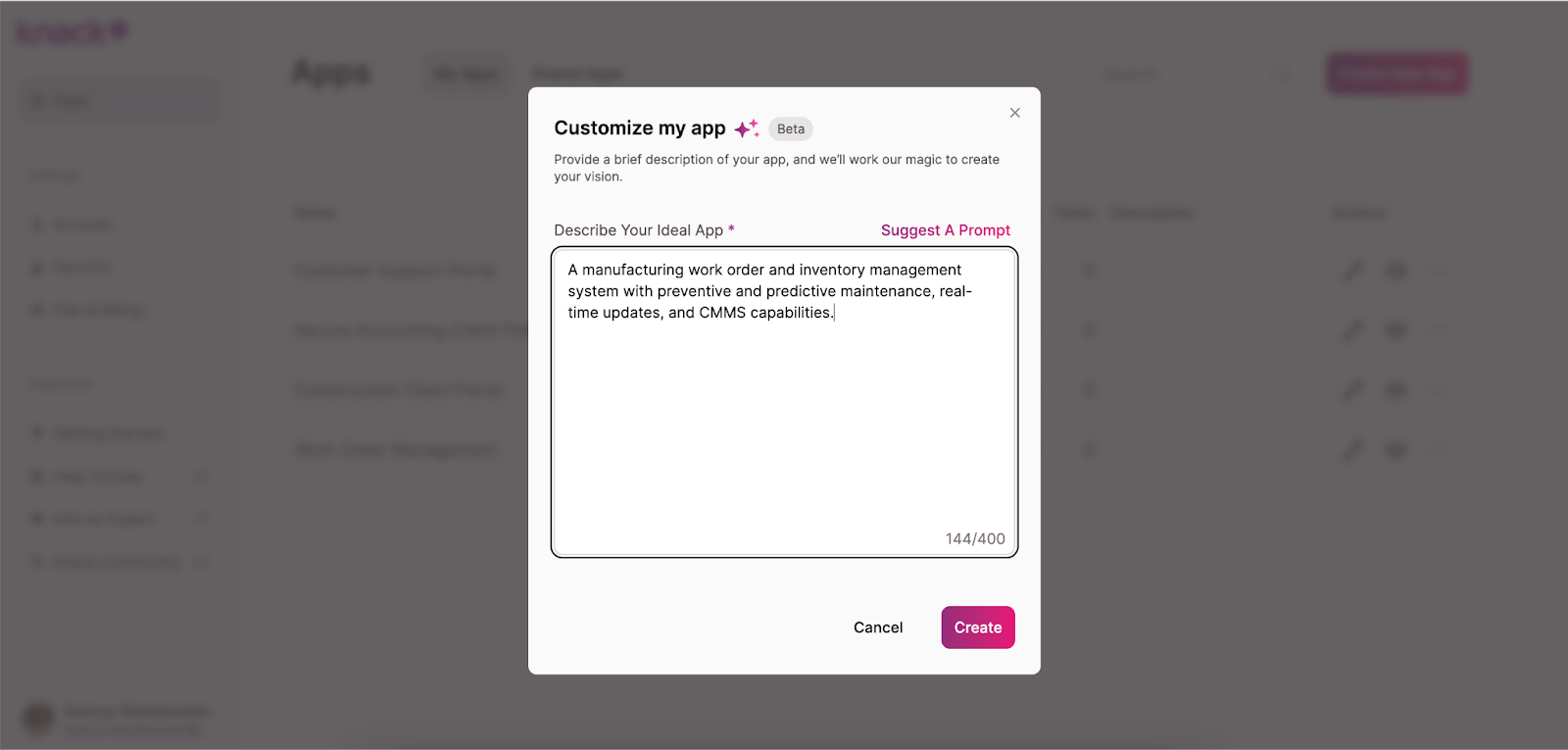
- Explore the suggested structure and edit it to fit your needs. Using the menu to the left, you can add, adjust, or remove tables, fields, connections, pages, and views. This is where all data will be stored, so make sure everything is organized and clearly labeled.
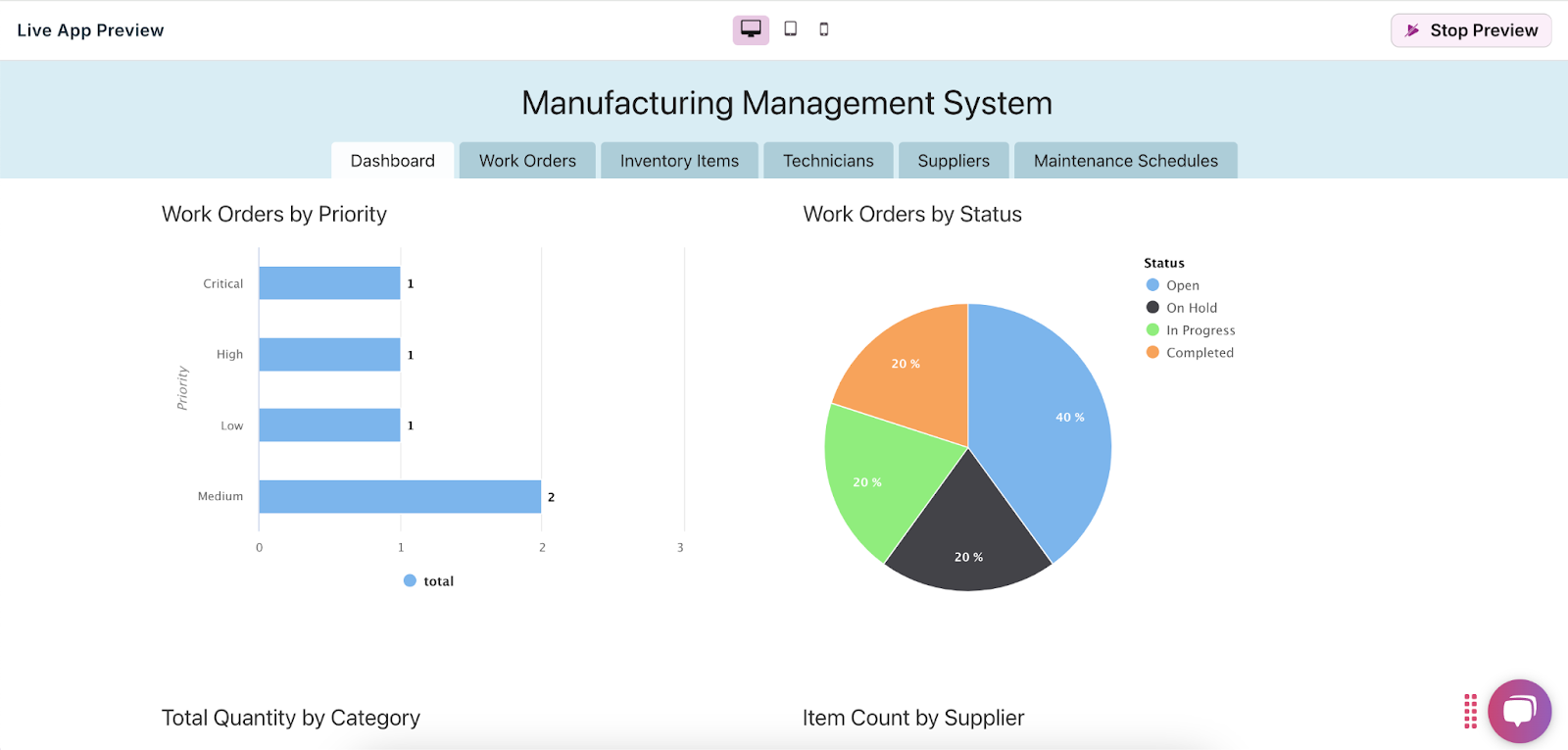
- Customize the user roles and permissions for each page by clicking the dropdown arrow and selecting “Require Login.” This allows you to choose who can access what information and functionalities.
- Add any necessary integrations, like accounting or CRM software, using the “API & Code” option in the “Settings” menu. For more guidance, read this Introduction to the API article.
- In the menu on the left side of the builder, click “Settings” and then “Live App Design” to customize the user interface. You can add your company logo, change fonts, select colors, and more to make the portal fit your brand.
- Navigate to the “Records” section and import any existing inventory data into your tables.
Option 3: Build From Scratch
If you want more control over your software, try building it from scratch. This may seem more complicated, but Knack’s intuitive interface makes it simple.
- In the top right corner of the app builder, click “Create New App” and then “Start from scratch.”
- Using the menu to the left, you can add, adjust, or remove tables, fields, connections, pages, and views. This is where all data will be stored, so make sure everything is organized and clearly labeled.
- Customize the user roles and permissions for each page by clicking the dropdown arrow and selecting “Require Login.” This allows you to choose who can access what information and functionalities.
- Add any necessary integrations, like accounting or CRM software, using the “API & Code” option in the “Settings” menu. For more guidance, read this Introduction to the API article.
- In the menu on the left side of the builder, click “Settings” and then “Live App Design” to customize the user interface. You can add your company logo, change fonts, select colors, and more to make the portal fit your brand.
- Navigate to the “Records” section and import any existing inventory data into your tables.
Performance Optimization Tools and Metrics in Leading Software
For your work order and inventory management software to remain effective, you have to monitor and optimize it.
Key Performance Indicators (KPIs) for Maintenance
Tracking key performance indicators (KPIs) is essential for understanding and optimizing maintenance operations. Metrics like mean time to repair (MTTR), asset reliability, and technician response time provide valuable insights into how efficiently maintenance tasks are handled. By identifying trends and pinpointing areas for improvement, businesses can enhance operational efficiency and ensure that maintenance processes support their broader goals.
Analytics for Informed Decision-Making
Analytics capabilities in top work order and inventory management software enable businesses to make informed, data-driven decisions. By analyzing trends, usage patterns, and performance metrics, teams can gain insights into their operations and identify opportunities for optimization. This data-centric approach provides a solid foundation for strategic planning that helps businesses enhance productivity and operational effectiveness.
Maintenance Cycle Insights and Inventory Levels
Understanding maintenance cycles and inventory levels is vital for ensuring that operations run smoothly without interruption. Top solutions offer tools to track maintenance schedules, monitor inventory levels, and forecast future needs based on historical data. This proactive approach to inventory and maintenance ensures that all resources are available when needed, minimizing disruptions and supporting consistent operational performance.
Enhancing Customer Satisfaction with Work Order Management Software
Work order management software benefits your business, but it also increases customer satisfaction through efficiency and responsiveness improvements.
Quick Response Times and Task Prioritization
Work order management software helps businesses meet customer expectations by prioritizing tasks based on urgency, ensuring that high-priority issues are addressed first. This capability allows teams to manage work orders efficiently, reducing delays and improving response times. By prioritizing tasks effectively and enhancing service quality, businesses can strengthen customer relationships and increase overall satisfaction.
Customizable Work Order Types for Flexibility
Different maintenance requirements call for varying levels of response, from routine preventive maintenance to emergency repairs. Advanced work order management software allows businesses to create custom work order types tailored to specific needs. This flexibility enables teams to categorize tasks based on urgency, type, or criteria, such as corrective, preventive, predictive, and emergency maintenance. By tailoring work order types to operational demands, businesses can maintain a more organized, responsive maintenance system.
Frequently Asked Questions (FAQs)
What is work order and inventory management software?
Work order and inventory management software is a system that helps businesses track and manage maintenance tasks, work orders, and inventory levels to streamline operations and improve efficiency.
Who benefits most from this software?
Facility managers, maintenance teams, and industries with complex asset management needs benefit the most from work order and inventory management software because it allows them to streamline workflows and improve efficiency.
What is CMMS, and why is it important?
A Computerized Maintenance Management System (CMMS) helps manage assets, schedule maintenance, and keep detailed equipment performance records. This is crucial for minimizing downtime and extending asset lifespans.
How does this software support compliance?
Work order and inventory management software support compliance by offering features such as customizable reports, audit trails, and data tracking that make it easier to adhere to industry regulations.
Conclusion: Try Knack’s Work Order and Inventory Management Software for Optimal Operations
Investing in reliable work order and inventory management software can transform the way businesses handle maintenance, asset management, and inventory tracking. Whether managing complex facilities or maintaining essential equipment, adopting a top-tier solution empowers teams to work more efficiently and respond quickly to operational needs.
Ready to build a fully functional work order and inventory management system tailored to your business needs? Sign up with Knack and start building for free today!